How do you find a quality apparel supply chain?
- Share
- publisher
- jane
- Issue Time
- Apr 19,2024
Summary
Looking for professional quality clothing manufacturers look for metrodress.
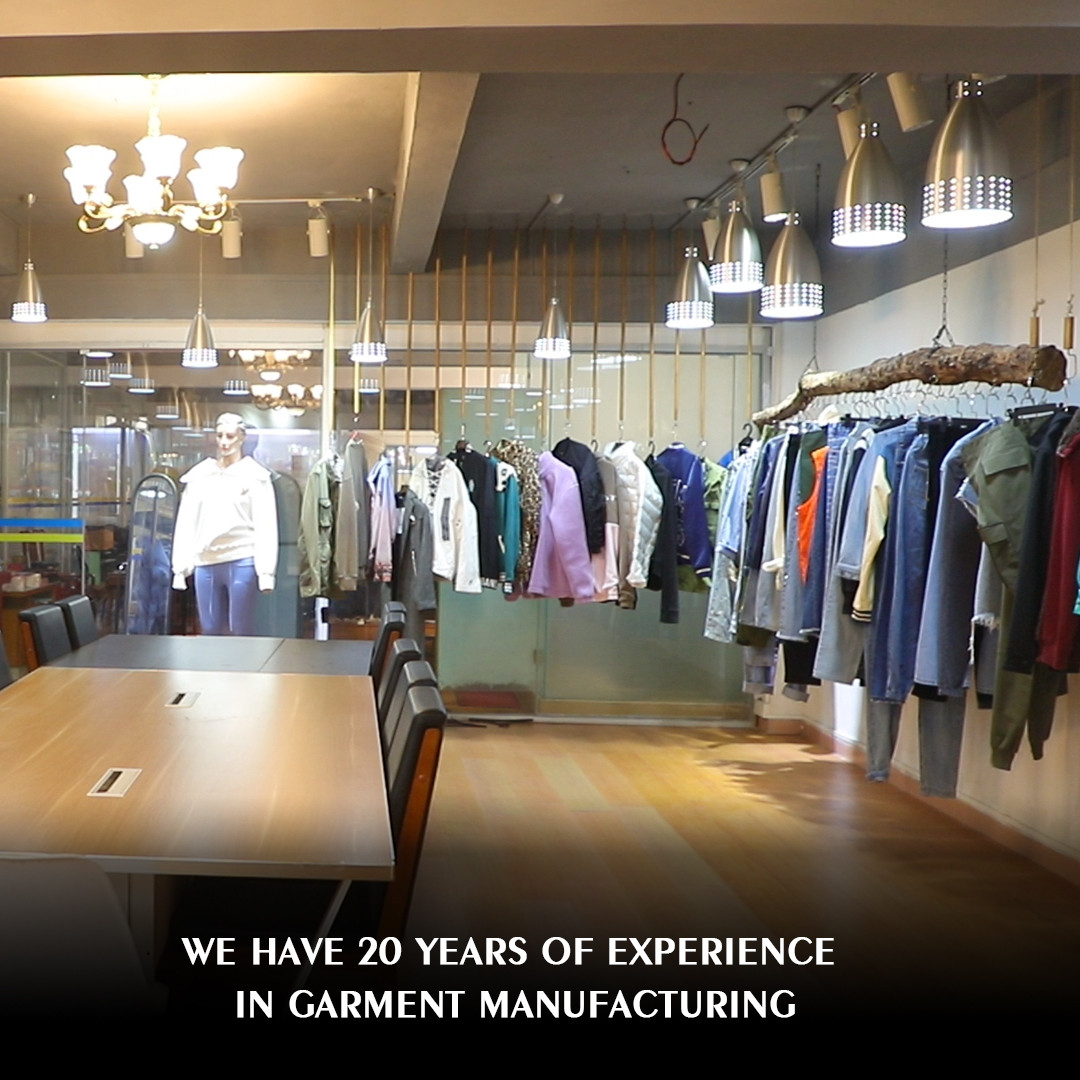
How to find a quality clothing supply chain?
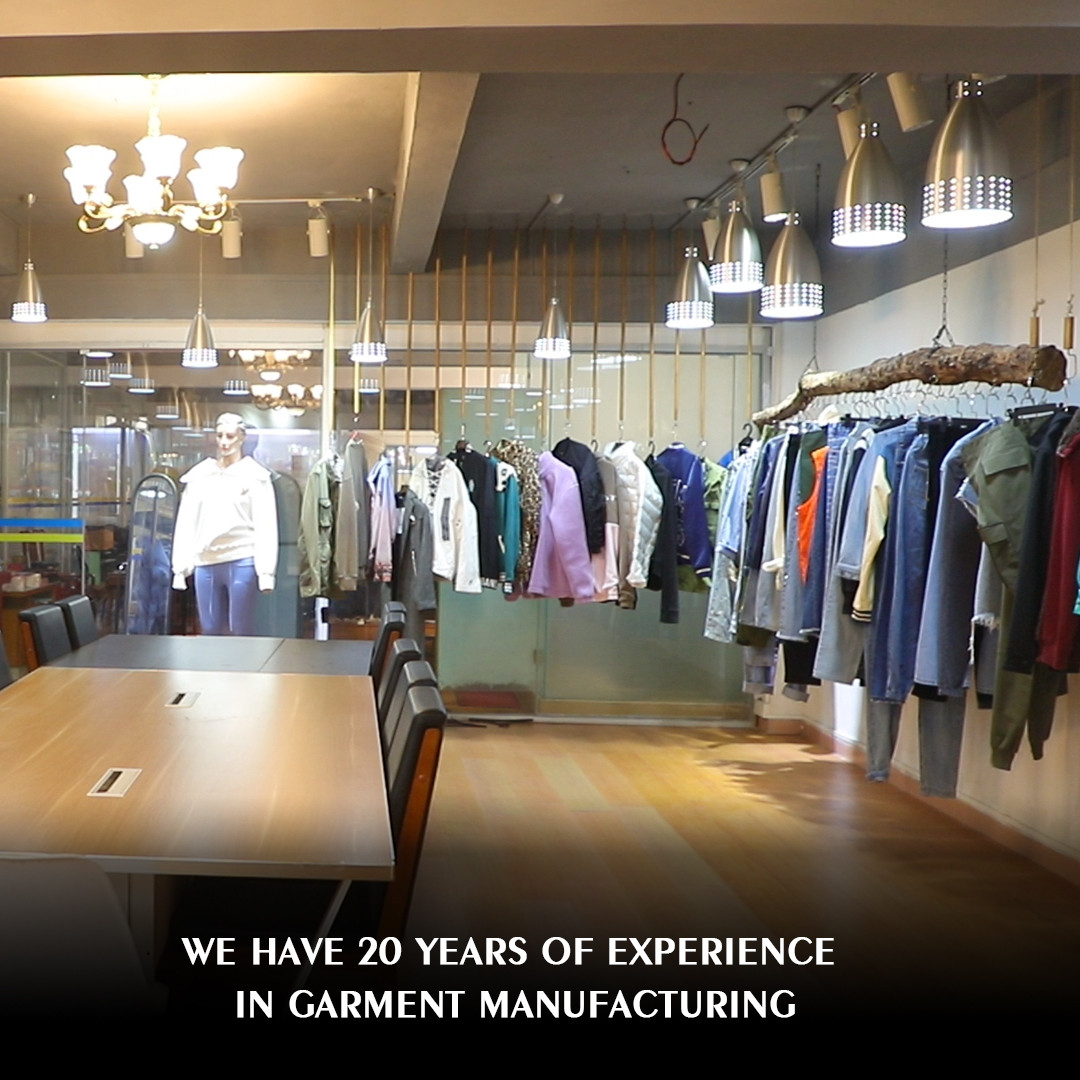
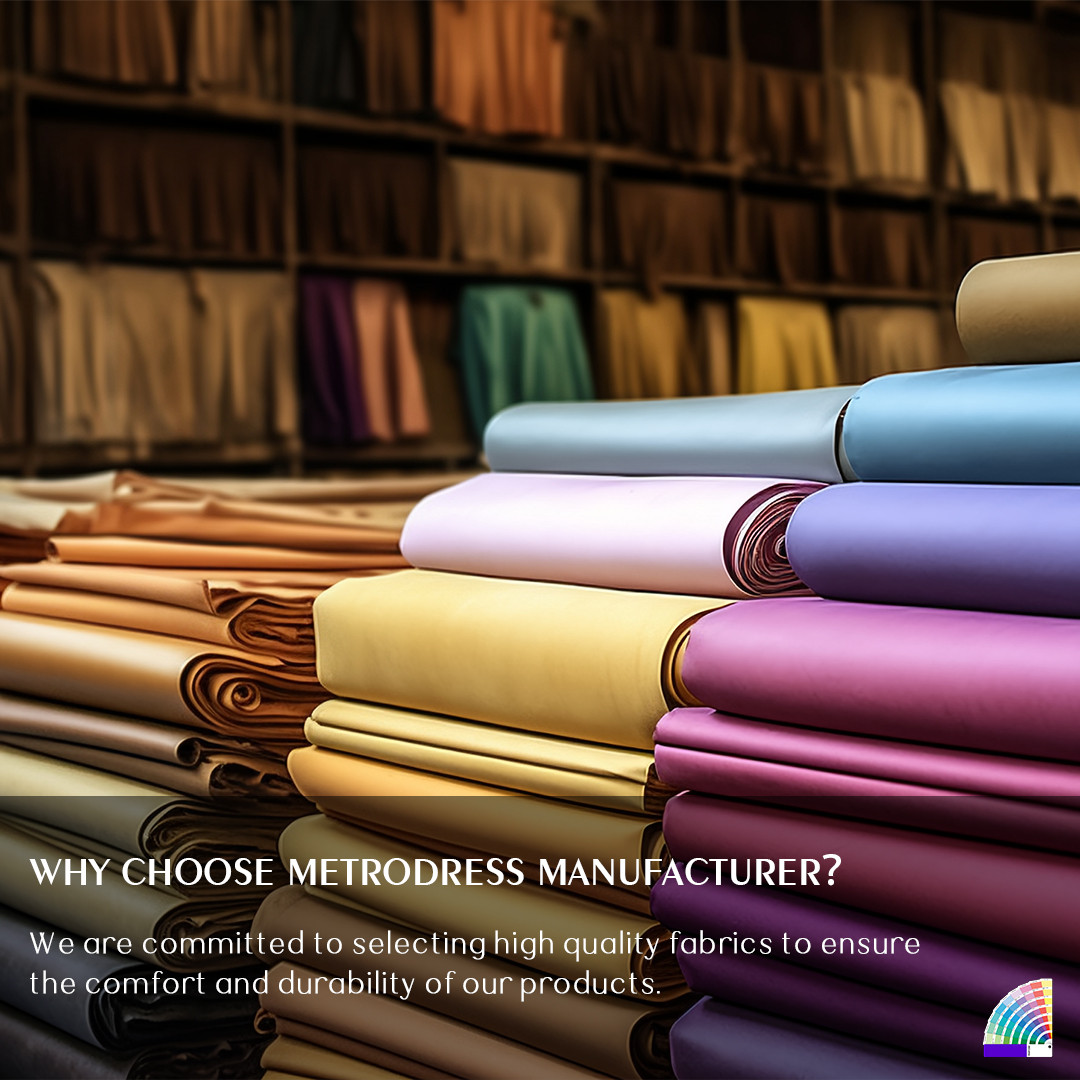
There are several key steps and considerations to finding a quality apparel supply chain:
Market Research:
Learn about the supply chain in the marketplace, including the key players in each segment, processes, and pricing. This can be done through online research, visiting trade shows, and speaking with industry insiders.
Set standards:
Determine the standards you need in a supply chain partner, such as production capacity, quality control, sustainability, etc.
Sourcing:
Sourcing can be done in a variety of ways, including through internet searches, attending trade shows, consulting with professional organisations, or by looking at the practices of other successful brands.
Background Checks:
Conduct background checks on potential suppliers, including checking their business records, reputation, credentials, and customer reviews.
Communication:
Comm unicate actively with potential suppliers to learn about their production processes, quality control measures, delivery times, etc.
Site visit:
If possible, it is best to visit the potential supplier's production site to understand the actual production situation and working environment.
Establishment of co-operation:
After selecting a suitable supplier, establish a solid co-operation relationship and sign a clear contract to ensure the rights and interests of both parties.
Ongoing Supervision:
Maintain ongoing supervision and communication during the co-operation process to ensure that all aspects of the supply chain are functioning as expected and that any problems that may arise are resolved in a timely manner.
Continuous Improvement:
Regularly assess the performance of the supply chain and continuously seek opportunities for improvement to increase efficiency and quality and reduce costs, while also focusing on aspects such as sustainability and social responsibility.
How to find a quality clothing supply chain?
Transparent Communication:
Honest communication is the foundation of a good relationship. Share your expectations, needs and goals and encourage manufacturers to share their ideas and suggestions as well. Communicating problems and seeking solutions in a timely manner helps build trust.
Build a mutually beneficial relationship:
Ensure that the relationship is a two-way street and that the manufacturer benefits as well. Offering reasonable pricing, a steady order book and a long-term commitment to working together can help build a strong, mutually beneficial relationship.
Respect and Understanding:
Respect manufacturers' expertise and experience, and understand their manufacturing processes and constraints. Avoid overreaching or imposing unreasonable requirements, and instead seek to work with them to find solutions.
Regular communication and liaison:
Regular communication and liaison with manufacturers not only helps to resolve issues, but also deepens understanding and trust between both parties. This can be done by telephone, email, video conferencing and many other means.
Reasonable time and deadline:
Give the manufacturer enough time to fulfil the order and make sure the deadline is reasonable. Avoid ad-hoc change orders or urgent requests unless they are truly necessary.
Build a strong relationship:
If possible, try to build a closer relationship, for example by inviting the manufacturer to your product development meetings or to visit your company. This will help to develop a better understanding and co-operation between the two parties.
Rewards and incentives:
Motivate manufacturers to provide you with better service and quality by offering rewards or incentives. This can include providing additional orders, long-term cooperation agreements or financial incentives.
Problem solving:
When problems arise, it's important to approach them with a problem-solving attitude rather than assigning blame or pointing fingers. Work together to find a solution and ensure that similar problems do not occur again.
Along with customisation and collaboration, we have to have our own customisation standards
Quality standards:
- Include requirements for product appearance, dimensions, materials, workmanship, and so on. You can refer to International Organisation for Standardisation (ISO) quality management standards, such as ISO 9001, or develop your own quality control standards.
- Safety standards:
- Ensure that products comply with relevant safety regulations and standards to protect consumers from safety risks. This may involve requirements for material selection, manufacturing processes, product testing, etc.
- Environmental standards:
- Aim to reduce the impact on the environment, including waste reduction, energy saving, the use of environmentally friendly materials and other requirements. Reference can be made to environmental management standards such as ISO 14001.
- Social Responsibility Standards:
- Ensure that manufacturers comply with minimum standards for labour rights, human rights, working conditions, etc. This may include prohibitions on child labour, forced labour, etc. This may include requirements to prohibit child labour, forced labour, discrimination, etc. Reference can be made to relevant International Labour Organisation (ILO) conventions or best practice in other industries.
- Traceability standards:
- Ensure that products can be traced back to their production processes and raw material sources to ensure quality and safety. This may involve requirements such as documenting the manufacturing process, batch traceability, supply chain transparency, etc.
- Sustainability Criteria:
- Aims to ensure that the production and use of a product minimises its environmental and social impacts. This may include requirements to use renewable materials, reduce energy consumption, and promote a circular economy.
- Industry-specific standards:
- Certain industries may have their own industry-specific standards and norms, such as food safety standards in the food industry and medical device quality management systems in the medical device industry.
Customised standards are usually tailored to the characteristics and requirements of your industry, and can be adapted and refined accordingly. When working with manufacturers, incorporating these customised standards into contracts and agreements and ensuring that both parties understand and comply with them can help to ensure product quality and a stable relationship.
Contact Metrodress
If you are looking for a reliable apparel manufacturer and are interested in our services, please contact us today. We will be happy to provide you with the best quality services and products to help your brand succeed!
Long white party dresses represent endless elegance and purity, long dresses add a modest and dignified.
Custom prom dresses,OEM dresses
Any oem service according to your needs.
Custom prom dresses,OEM dresses
Any oem service according to your needs.
Custom prom dresses,OEM dresses
Any oem service according to your needs.